Co-Authored By:
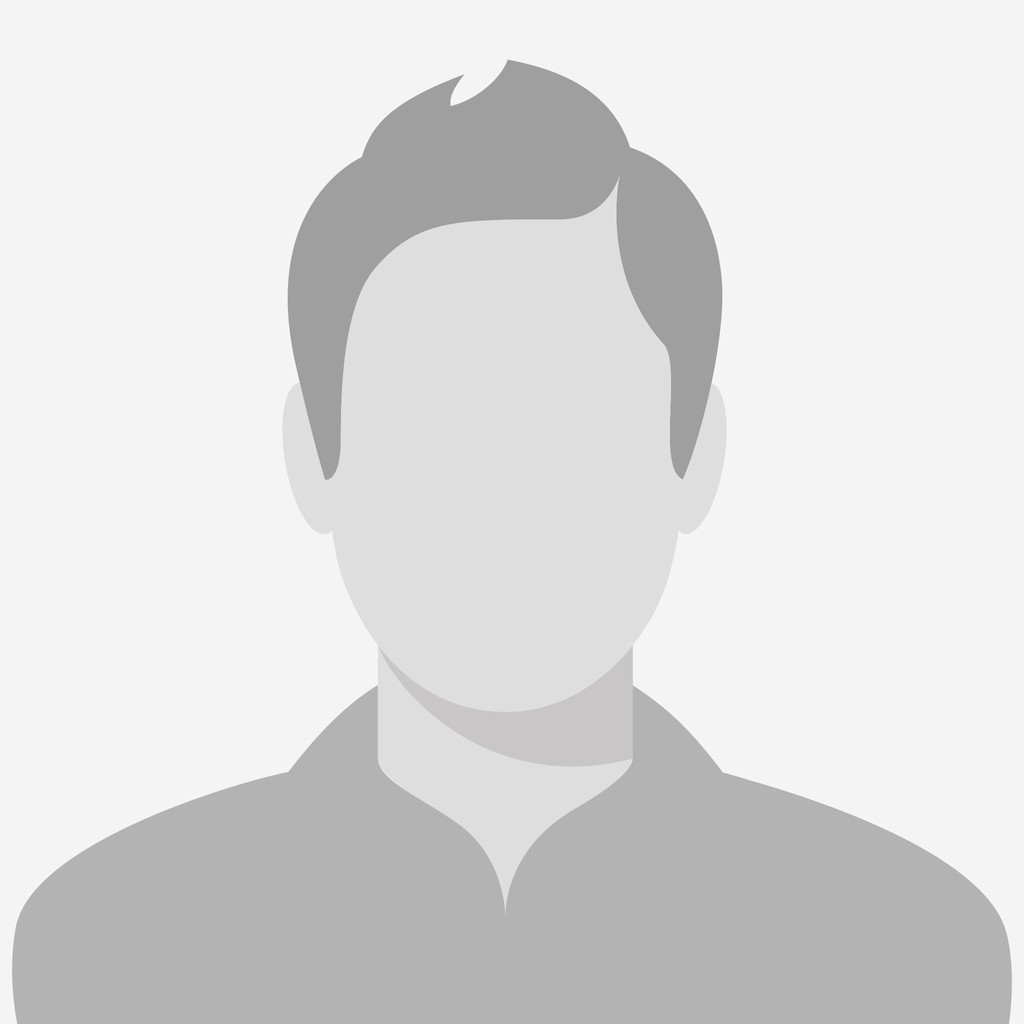
Asked by: Quinti Mommerz
business and finance manufacturing industryHow do you find the minimum number of workstations?
Calculate the theoretical minimum number of workstations. NUMBER OF WORK STATIONS = ( SUM OF TOTAL TASK TIMES) / (CYCLE TIME)= 70 min's / 15 min's = 4.67 ≈5 (rounded) Number of Task Following Tasks STEP 4.
In this regard, how do you calculate minimum cycle time?
a. Minimum cycle time = length of longest task, which is 2.4 minutes. Maximum cycle time = ? task times = 18 minutes. b.
- Available Minutes for Production / Required Units of Production = Takt Time.
- 8 hours x 60 minutes = 480 total minutes.
- 480 – 45 = 435.
- 435 available minutes / 50 required units of production = 8.7 minutes (or 522 seconds)
- 435 minutes x 5 days = 2175 total available minutes.
how do you calculate delay in balance?
The balance delay is the percentage of wasted time or 100% - the efficiency. In this example, it is 4 (the idle time)/30 or . 1333, which is also determined by 1-. 8667.
So the simplest way to measure the cycle time of an assignment is to count the number of days it spent being worked on. In other words, if you start a task on the 15th of April and complete it on the 25th of April, then the cycle time is 10 days.