Co-Authored By:
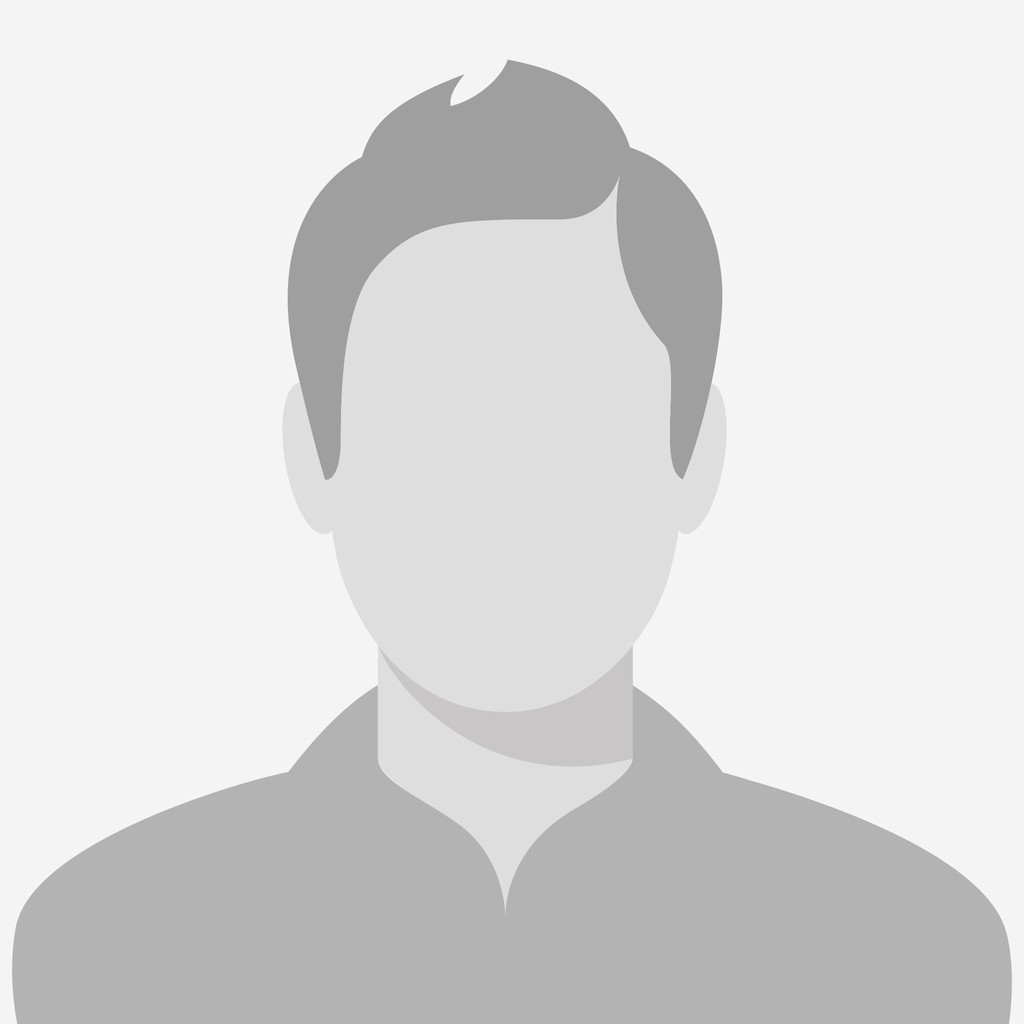
Asked by: Edelweiss Monnig
business and finance food industryWhat are the disadvantages of extrusion?
Also know, what are the advantages of extrusion process?
The two main advantages of this process over other manufacturing processes are its ability to create very complex cross-sections, and to work materials that are brittle, because the material only encounters compressive and shear stresses. It also forms parts with an excellent surface finish.
Also Know, what are the advantages and disadvantages of injection Moulding?
Plastic injection moulding advantages centre around great precision and high repeatability, combined with speed, a low cost per part and a huge choice of available plastics. Disadvantages include a higher initial cost and lead time than some other processes.
Cold extrusion is also defined as a compressive forming process (push-through), where the starting material is billet / slug and the process is carried out at the room temperature. During the cold extrusion process, deformation heating of the deforming material takes place at several hundred degrees.